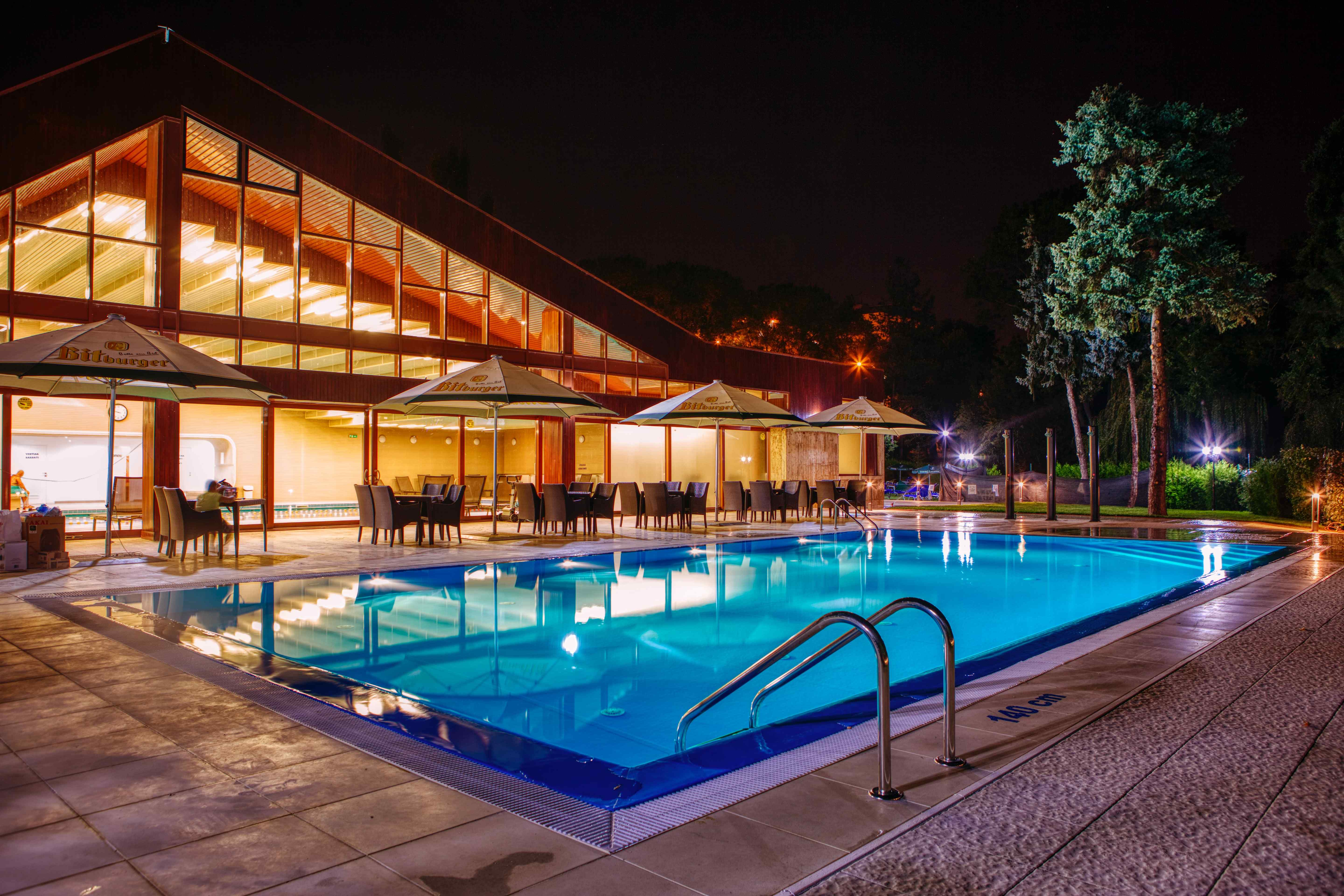
Continuing Education: Structural Bamboo
By now, the oft-repeated stats should be familiar: the built environment contributes nearly 40 percent of the greenhouse gases emitted annually, and at least one-quarter of that is embodied carbon, or the emissions associated with the manufacture of products used to make buildings and with the construction process. So how can we continue to build while minimizing these impacts? One answer is to use bio-based materials. And one such material—with untapped potential—is bamboo. It is abundant, has a rapid growth cycle, and is strong, sometimes characterized as vegetable steel.
What exactly is bamboo? Bamboo is often thought of as wood, but the plants are not trees. Instead, they are part of the grass family. More than 1,600 species exist, with most tending to thrive in humid climates close to the equator. These are divided into herbaceous types, which are slender-stalked and grow as understories, and the larger-diameter “woody” varieties more suitable for construction. Some have “running” root systems, which can send up new shoots as far as 100 feet from an existing culm (or stem), while others clump, growing new culms close to the base of an existing one.
Bamboo is made up of nodes that segment the culm and act as diaphragms, preventing the otherwise hollow plant from buckling. In between run vascular bundles and cellulose fibers, providing bamboo with excellent performance along its axis in compression, bending, and especially tension. “If I imagined an ideal structural material, it would be bamboo,” says Neil Thomas, founder and director of the London-based engineering firm Atelier One.
Of course, bamboo has been used as a construction material for thousands of years. But one reason it is attracting more attention now is its ability to store carbon. According to the International Bamboo and Rattan Organization (INBAR)—an intergovernmental group that promotes development using those two materials—bamboo ecosystems contain between 94 and 392 metric tons of carbon per hectare (tC/ha), depending on species, soil conditions, geography, and other factors. Although this is markedly less than the carbon captured by natural forests, which contain between 126 and 699 tC/ha, it is comparable to that of tree plantations. In addition, points out INBAR, unlike most tree species, many types of bamboo can be grown on degraded land, helping satisfy the dual goals of soil restoration and carbon sequestration.
From a climate-solution standpoint, bamboo’s most remarkable attribute is its quick maturation and regeneration cycle. Bamboo can be harvested within three to seven years of sprouting, with the same clump producing multiple harvests. (According to some estimates, a single bamboo clump can produce up to nine miles of usable culm over a 15-year period.) This growth pace means, that compared to most tree species, bamboo plants generally have higher yields and higher storage of carbon when they are used to make buildings or long–life span products. Over a 30-year period, the carbon-storage potential of durable products made from guadua, a South American bamboo species, is 134.7 tC/ha, compared to only 30.0 for Chinese fir, says INBAR.
The material does have its limitations, however, especially when used in its natural state. Without proper precautions, bamboo is susceptible to moisture, insect infestation, UV degradation, and—because the culms are hollow—they pose a high fire risk. And, though bamboo buildings are often cited for their ability to survive earthquakes because of their flexibility, this is a bit of a misconception, says Sebastian Kaminski, an associate structural engineer in the London office of Arup. Bamboo buildings have historically performed well in quakes primarily because bamboo has a high strength-to-weight ratio, which generally results in lightweight buildings, and seismic loads are proportional to mass, he explains.
For the last 14 years, Kaminski has been working to address bamboo’s shortcomings, and enhance the durability and livability of bamboo buildings, offering them as a solution for affordable and disaster-relief housing across the global south. Among his bamboo-related projects is an INBAR design guide, created with collaborators from academia and practice. It outlines a structural system that builds upon the wattle-and-daub construction methods still used in much of the developing world, incorporating modern materials and techniques.

Bamboo buildings can be durable when properly executed. This CBSW house in Costa Rica had been standing 20 years at the time of the photo. Photo © Arup
The improved version of the vernacular, known as a composite bamboo shear wall (CBSW), or engineered bahareque—as the traditional system is called in some regions of Latin America—is well-suited for one- and two-story structures in rural settings or in city outskirts, says Kaminski. The assembly sits on reinforced-concrete foundations supporting a masonry upstand, to elevate the bamboo frame above the ground. A matrix of cane or small-diameter bamboo, or bamboo lath, is nailed to one or both sides of the frame, and then galvanized-wire mesh is affixed as reinforcement. The final layer is a coating of cement mortar. By adding such details as generous roof overhangs to protect against the driving rain, use of bamboo treated with the chemical element boron to guard against insect infestation, a minimum thickness of the mortar for fire protection, and proper seismic connections, a CBSW building can be robust and last for as long as 50 years, says Kaminski. And, notably, the embodied carbon of a structure relying on such a system is less than half of one using more conventional manufactured materials, like concrete masonry, that are typical in humanitarian housing. “That is even before taking into account the biogenic carbon,” he says, referring to the carbon stored within the bamboo. Thus far, the CBSW has been sanctioned by the building codes of Colombia, Ecuador, and Peru, as well the International Organization for Standardization (ISO). Efforts are also under way to incorporate it into the Philippine, Mexican, and Nepalese building standards.

Click drawing to enlarge Courtesy of Arup
In Indonesia, bamboo is part of the culture, notes Defit Wijaya, lead architect at Bali-based design firm IBUKU. But now the studio, which focuses almost entirely on bamboo, is creating a new formal vocabulary for the ages-old material. One emblematic project is the Arc, a gymnasium at the Bali campus of the Green School, a pre-K through 12th-grade independent school. The product of a collaboration with Colombia-based bamboo specialist Jörg Stamm and Atelier One, the 8,000-square-foot building has no walls, in keeping with the school’s nature-focused mission. But it is sheltered under a striking sculptural roof, 118 feet long and 45 feet tall at its highest point, that seems to recall some extinct armored mammal. The structure, made primarily of the bamboo species Dendrocalamus asper, or Bambu Petung, is supported by a series of interlocking arches, each a bundle of culms rising from concrete pedestals and spanning 65 feet. Between them, crisscrossing bamboo splits form doubly curved gridshells topped with a waterproofing membrane. The whole is topped with a layer of plupuh, or shingles of flattened bamboo.

1
Crisscrossing bamboo splits (2) running between arches of bundled bamboo (1) make up the Arc’s doubly curved gridshells. Images courtesy of Ibuku (1), Tommaso Riva (2), click to enlarge.

2
Because the roof’s structure of anticlastic, or oppositely curving, gridshells was unprecedented in such a natural and highly variable material, the project demanded a unique approach. Wijaya describes a process in which design, engineering, and testing were happening nearly concurrently, and in both digital and analog realms. The team used drawings, physical models, and computer simulations to develop and refine the scheme. They also heavily relied on full-scale mockups of the arches and other elements, loading them with concrete blocks to understand their bearing capacity. A bamboo culm “is not like a wood joist, which is normalized and graded. You know what it is and what it does. This is nature,” says Thomas of the challenges of building with bamboo.

Full-scale physical tests helped designers understand the loading capacity of the Arc’s structural elements. Photo © James Wolff, PT Bamboo

The Arc’s bamboo arches rise from concrete pedestals. Photo © Tommaso Riva
This complexity is one reason bamboo as a structural material—at least in its natural state—is unlikely to make significant inroads in the U.S. But Seattle-based structural engineer Don Davies, cofounder of Davies-Crooks, a consulting practice focused on lowering climate impacts, does see a role for bamboo in North American construction. He argues for an approach he calls “fiber optimization,” which means, he says, using the best and most appropriate material for each load application, while taking into account carbon emissions and other environmental considerations. As one of nature’s fastest-growing fibers, bamboo could be used to great advantage, he says, if fabricated into familiar shapes and sizes, with predictable performance, even as hybrids with other materials such as timber.
A handful of companies have entered the U.S. market with the kind of structural bamboo products that Davies is advocating. One is Windsor, California-based BamCore, which offers a panelized shear-wall framing system for low-rise residential and commercial construction. It typically consists of two engineered sheets, combining wood and bamboo plies, on either side of a shallow cavity. With bamboo sourced primarily in Central America, the company manufactures the sheets in Ocala, Florida, and then fabricates the structural panels—complete with openings for windows, doors, and mechanical systems—either there or in its California facility. The company also has plans to offer a mass-timber-bamboo product within the next 18 months, which it says will be thinner, stiffer, and lighter than cross-laminated timber.
Architecture firm, BLDUS, a 2023 Record Vanguard, has used BamCore’s shear-wall system in several projects, including its own office in the Anacostia neighborhood of Washington, D.C. Dubbed the Grass House—a play on the name of Philip Johnson’s New Canaan, Connecticut, residence, but also a reference to bamboo’s plant family—the 750-square-foot, two-story (plus basement) structure has exterior walls framed in BamCore panels. The framing system is used in the diminutive building along with other rapidly renewable, bio-based materials, including mycelium and woven willow, “because we are concerned about how our product choices impact the earth and the health of the building’s inhabitants,” says principal Andrew Linn, who founded BLDUS with Jack Becker in 2013.

3
The exterior walls of the Grass House (3), in Washington, D.C., are framed in composite bamboo-wood panels. The wood face of the panels is exposed on the interior (4). Photos © Ty Cole

4
Technically an accessory structure to the neighboring Victorian house where Becker lives, the prefabrication of the panels made construction faster and simpler on the tight site, compared to standard wood framing, says Linn. The architects specified lambswool insulation for the 5½-inch cavity within the panels, while the absence of studs meant reduced heat loss through thermal bridging. The framing system also allowed elimination of some finishes—namely drywall on the interior—along with their corresponding embodied carbon. Here the architects left the inside face (a layer of wood) exposed, but stained it various shades of brown. Because the panel’s outside face requires protection from the elements, Becker and Linn covered it with a fluid-applied waterproof membrane, and then clad the structure in local black locust.
Along with BamCore, there are a few other pioneers of structural engineered bamboo (SEB) offering their products in the U.S., including Lamboo, Renuteq, and Moso. They make a variety of structural and semi-structural products, such as columns, beams, curtain-wall systems, and framing for structural glass. But the SEB industry is still in its infancy. If it is to scale up, says Davies, more support is needed for early adopters. “Opening a plant takes capital and time, which involves risk,” he says.
If, and when, SEB takes off, even the most ardent bamboo fans see it as a complement, rather than a replacement, for wood, steel, or concrete. “We need to combine the best bits of each material, each for their own properties,” says Thomas, echoing Davies’s thoughts on fiber optimization. Regardless of what combinations manufacturers and project teams come up with, let’s hope it is a big part of our material future, since the construction industry sorely needs more rapidly renewing and carbon-storing options.
Continuing Education

To earn one AIA learning unit (LU), including one hour of health, safety, and welfare (HSW) credit, read the article above and “Structural use of bamboo: Part 1: Introduction to bamboo”, Structural Engineer, August 2016, by Sebastian Kaminski, David J. Trujillo, and Andrew Lawrence.
Then complete the quiz. Upon passing the quiz, you will receive a certificate of completion, and your credit will be automatically reported to the AIA. Additional information regarding credit-reporting and continuing-education requirements can be found at continuingeducation.bnpmedia.com.
Learning Objectives
AIA/CES Course #K2309A
Complete the QuizIntroducing Jobbguru: Your Gateway to Career Success
The ultimate job platform is designed to connect job seekers with their dream career opportunities. Whether you're a recent graduate, a seasoned professional, or someone seeking a career change, Jobbguru provides you with the tools and resources to navigate the job market with ease.
Take the next step in your career with Jobbguru:
Don't let the perfect job opportunity pass you by. Join Jobbguru today and unlock a world of career possibilities. Start your journey towards professional success and discover your dream job with Jobbguru.
Originally posted on: https://www.architecturalrecord.com/articles/16452-continuing-education-structural-bamboo